In Fertigungsprozessen und an jeder Maschine fallen jede Menge Daten an, die oft nicht genutzt werden. Erfasst man Maschinendaten systematisch und verknüpft sie in Echtzeit mit der MES- und ERP-Welt, lassen sich wertvolle Informationen und Erkenntnisse gewinnen, beispielsweise zur optimalen Auslastung der Maschinen, zu Frühindikatoren von Qualitätsabweichungen, zur vorbeugenden Instandhaltung, zur Rückverfolgbarkeit (traceability) oder für Prozessoptimierungen.
Wir fragten Andreas Buchem, einer der drei Geschäftsführer der IDAP Informationsmanagement GmbH, warum Unternehmen mit diskreter Fertigung ihre Maschinen- und Prozessdaten nutzen sollten, wie man diese ohne riesige Investitionen vernetzen kann, welche Rolle Automatisierungslösungen, KI-Services und MES-Werkzeuge dabei spielen und wie Produktionsunternehmen derartige Vorhaben umsetzen können.
Herr Buchem, warum sollten Produktionsunternehmen mit diskreter Fertigung ihre ungenutzten Maschinen- und Prozessdaten auswerten?
Andreas Buchem: In vielen Fertigungsverfahren sind gerade die Prozess- und Umgebungsparameter entscheidend für das Ergebnis und die Qualität. Aus unserer Sicht verzichten noch zu viele Unternehmen darauf, aus diesen Daten die notwendigen Informationen zu generieren, um Fehler und Fehlleistungsaufwände frühzeitig zu erkennen und zu vermeiden.
Es geht aber auch um eine möglichst genaue Leistungserfassung, um eine größtmögliche Kosten-Transparenz herzustellen. Mit den richtigen Systemen und systemübergreifendem Prozess-Design können beide Ziele erreicht werden.
Welche Informationen und neuen Erkenntnisse sind zu erwarten?
Häufig haben die Unternehmen schon ein Gefühl dafür, wo es im Prozess zu unerwünschten Qualitätsabweichungen kommt. Nur können sie es anhand der Datenlage nicht nachvollziehen.
Das Ziel sollte sein, die kritischen Parameter zu ermitteln, zu überwachen und dann in Korrelation zu setzen.
Welche Voraussetzungen und Integrationsleistungen muss man erfüllen, bis man so weit ist?
Man wird nicht auf einen Schlag alle Parameter erfassen können. Also muss man sich sukzessive an den Idealzustand heranarbeiten. Wie bereits erwähnt, kennen die Unternehmen häufig schon ihre Problemzonen. Daraus ergeben sich die Prioritäten für eine Reihenfolge der Aktivitäten. Dann ist der jeweilige Prozess-Schritt zu analysieren.
Im Rahmen einer Analyse, beispielsweise einer FMEA (Fehlermöglichkeits- und Einflussanalyse) sollten alle Einflussfaktoren eines Prozess-Schrittes ermittelt werden. Dann ist zu prüfen, welche Faktoren auf welche Weise ermittelt werden können.
Idealerweise können viele Faktoren (Temperaturen, Geschwindigkeiten, Drücke, verwendete Werkzeuge u.v.m.) per Sensorik ermittelt und per MES erfasst werden. Manche Faktoren müssen gegebenenfalls manuell erfasst werden, wenn es keine maschinelle Möglichkeit geben sollte.
Wie kann man die Komplexität bei der notwendigen Vernetzung von Maschinendaten, SAP und MES reduzieren, damit sich derartige Vorhaben rechnen?
Für das Thema der Sensorik und damit verbunden auch die Anbindung von Maschinen gibt es heutzutage standardisierte Protokolle und Hardware. Das reduziert die Komplexität bereits erheblich.
Darüber hinaus geht es in puncto Schnittstelle vor allem um Flexibilität und Offenheit. Die Lösung von der Stange gibt es nämlich nicht. Es geht immer um spezifische Lösungen.
Beim Gießereiunternehmen Gienanth Group haben Sie vollautomatische Gießanlagen angebunden und das Prozessdaten-Management für mehrstufige Produktionsprozesse realisiert. Was hat das Unternehmen davon?
Auf den Punkt gebracht: Mehr Prozesskontrolle und neue Ansätze für die Prozessoptimierung. Ein Beispiel: Die mit der SPS-Maschinensteuerung vernetzten Sensoren erfassen unter anderem den Druck im Gießofen. Damit wird die Zeit seit dem letzten Einfüllen des Flüssigeisens überwacht.
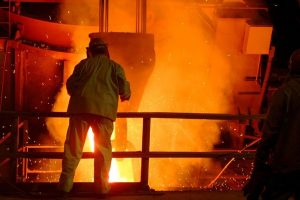
Eine zu lange Standzeit würde sich negativ auf die Qualität der Schmelze auswirken. Und die ist in einer Gießerei von entscheidender Bedeutung. Grenzwertüberschreitungen werden über Warnleuchten optisch signalisiert und dem verantwortlichen Mitarbeiter zugleich über das System gemeldet.
Beides, die Meldungen und die Durchführung der für diesen Fall vorgegebenen Maßnahmen, nämlich die Schmelze aufzufrischen, müssen quittiert werden. Zudem kann über ein Cockpit jederzeit, von überall und mit jedem Endgerät auf sämtliche Maschinenzustände, Prozesswerte und Rückmeldedaten zugegriffen werden.
Insgesamt wird so eine Reaktion möglich, noch bevor Probleme auftreten. Das hilft Ausschuss, Produktionsstillstände und Schäden an den Anlagen zu vermeiden.
Welche Empfehlungen geben Sie anderen Unternehmen, die ähnliche Vorhaben planen?
Die Erfassung von Prozessdaten ist kein Selbstzweck. Es geht nicht darum, Daten zu erfassen, nur weil es technisch möglich ist. Wie erwähnt, sollte man hier im Vorfeld eine Analyse durchführen und eine klare Strategie erarbeiten.
Letztendlich unterliegt alles einer Kosten-Nutzen-Abschätzung. Dort, wo die Effekte am größten erwartet werden, sollte auch begonnen werden.
Eine Frage noch: Automatisierung von Routineaufgaben und die Nutzung von KI sind derzeit in aller Munde. Welche Rolle spielen diese Innovationsthemen in der Fertigung?
Das Automatisieren von Routineaufgaben ist ja keine neue Entwicklung. Es gibt aber noch eine ganze Reihe von Routinetätigkeiten, die auch zukünftig weiterhin von Menschen durchgeführt werden, weil hier entsprechendes Geschick und Flexibilität gefragt sind.
Hierbei können Systeme den Werker unterstützen, relevante Daten erfassen und Entscheidungshilfen geben. Das Thema KI ist definitiv ein Hype-Thema. Jedoch geht es hier auch weniger um das Wegrationalisieren von Arbeitsplätzen. Schätzungen zufolge sind lediglich 5 Prozent der Arbeitsplätze durch KI gefährdet. Im produzierenden Gewerbe wahrscheinlich noch weniger.
Aber die Art und Weise wie wir arbeiten wird sich verändern, beispielsweise die Zusammenarbeit von Mensch und Maschine oder die Unterstützung in Entscheidungsprozessen durch lernende Algorithmen.
Vielen Dank für das Gespräch.
Die Fragen stellte Helge Sanden, Chefredakteur des IT-Onlinemagazins.
ANZEIGE
Fachtagung WAGO & IDAP 2019:
Maschinendaten in die MES- und SAP-Welt integrieren – verblüffend einfach!
15.10.19 in Minden